纳米氧化锌生产:通过控制回转窑内氧分压与冷却速率,制备粒径 20-50nm 的球形颗粒;石墨烯负载金属催化剂:在回转窑内通氢气还原,实现金属颗粒(如 Pt、Pd)均匀分散在石墨烯片层;技术优势:连续化生产效率比间歇式炉提高 5-8 倍,产品批次稳定性 RSD<3%。模块化结构拆分:将窑体分为进料段、加热段、冷却段,各模块在工厂预制完成;快速安装工艺:采用液压顶升系统,现场安装周期从 60 天缩短至 25 天;应用场景:应急危废处理项目(如地震灾区医疗废物处置);海外 EPC 项目(减少现场施工人员 70%,降低海外用工风险)。回转窑的传动齿轮箱采用强制润滑与油液在线过滤,延长齿轮寿命并减少磨损颗粒。常州中温回转窑生产厂家
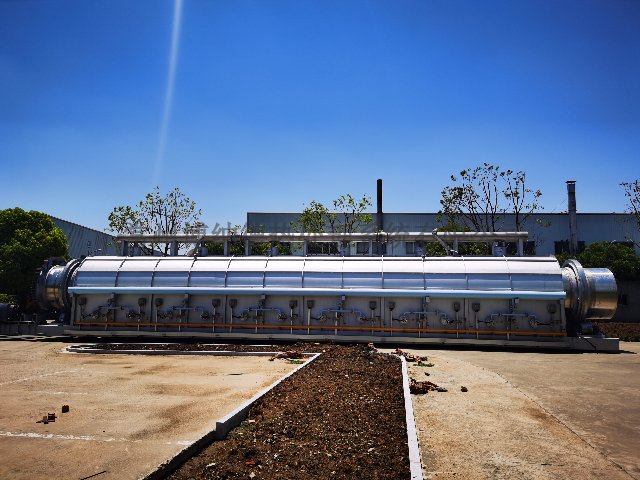
尾气处理系统解析:SNCR 脱硝 + 布袋除尘 + 湿法洗涤,使 HCl、重金属等指标优于国标;灰渣稳定化技术:螯合剂添加量对铅、镉浸出浓度的影响实验数据;某医疗废物处理项目案例:二噁英排放浓度<0.1ng TEQ/m³,远低于欧盟标准。磷酸铁锂正极材料煅烧:回转窑连续化生产效率比箱式炉提升 3 倍,能耗降低 25%;三元前驱体焙烧:通过控制窑内氧分压,精细调控镍钴锰比例偏差<1%;钠离子电池硬碳负极材料活化:回转窑内通 CO₂气体,比容量达 350mAh/g 以上。常州中温回转窑生产厂家有色金属回转窑的窑尾烟气余热可驱动汽轮机发电,实现能源循环利用与降本增效。
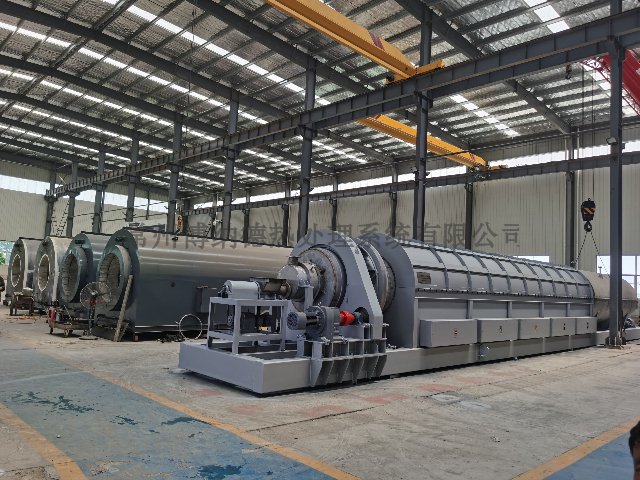
余热回收:窑尾烟气余热发电,吨水泥发电量达35kWh;低氮燃烧:分级燃烧技术将NOx排放从800mg/m³降至300mg/m³以下;碳捕捉:水泥回转窑CO₂捕集技术试点,年封存CO₂超万吨。解读“双碳”目标下,回转窑行业的技术升级路径。锂电池回收:正极材料经回转窑焙烧后,锂浸出率提升至 90% 以上;陶粒生产:城市污泥与粉煤灰在回转窑内烧结成轻质陶粒,用于建筑骨料;活性炭活化:木屑在回转窑内通水蒸气活化,比表面积达 1500m²/g 以上。
分区加热技术:传统的回转窑加热方式通常是整体加热,难以实现对不同区域的控制。而分区加热技术将窑体划分为多个加热区域,每个区域可以根据物料的热解阶段和温度需求进行控制。例如,在锂电池热解的初期,物料需要较低的温度进行干燥和预热,此时可以只启动窑体前端的加热区;随着热解过程的深入,逐步提高后端加热区的温度,使物料在不同的温度梯度下完成分解反应,提高热解效率和产品质量。电磁感应加热:电磁感应加热技术在锂电池回转窑中的应用逐渐受到关注。与传统的电加热或燃料加热相比,电磁感应加热具有加热速度快、能量转换效率高、温度控制精确等优点。通过在窑体内部或外部设置电磁感应线圈,利用电磁感应原理直接对物料进行加热,减少了热量在传递过程中的损失。此外,电磁感应加热还可以实现快速升温或降温,适应不同锂电池材料的热解工艺要求。水泥回转窑的窑筒体表面温度监测系统可通过红外热像仪实时扫描,局部过热隐患。
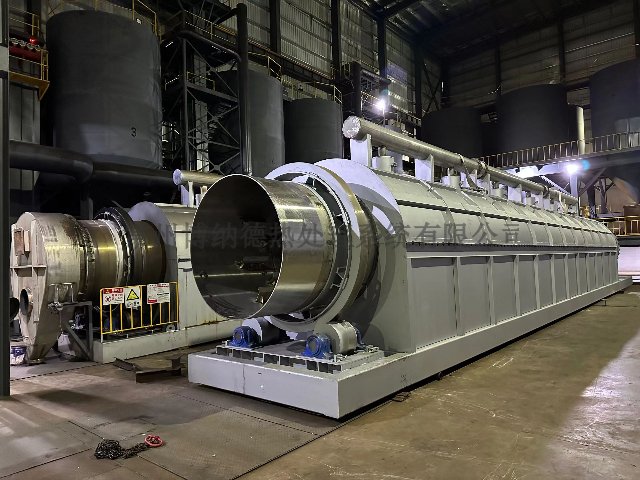
水泥回转窑:全球 90% 以上的水泥熟料通过回转窑生产,大型窑产能可达每日 1.2 万吨,搭配悬浮预热器与分解炉后,热耗从 1200kcal/kg 降至 750kcal/kg 以下。石灰回转窑:煅烧石灰石生产生石灰(CaO),用于钢铁脱硫、污水处理,其产能比传统竖式窑高 2-3 倍,且可处理 10-50mm 小颗粒原料。镍铁冶炼:红土镍矿经回转窑干燥焙烧后,电炉熔炼效率提升 20%,镍回收率超 90%;固废处理:钢厂除尘灰通过回转窑还原挥发,锌、铅等金属回收率达 85% 以上,实现 “变废为宝”。回转窑的托轮表面经耐磨处理,配合自动润滑系统,延长设备使用寿命并降低维护成本。常州中温回转窑生产厂家
水泥生产中的回转窑通过燃料燃烧释放高温,将生料煅烧成具有胶凝特性的熟料。常州中温回转窑生产厂家
某锂电池材料生产企业利用回转窑生产磷酸铁锂材料。在生产过程中,采用单层回转窑对磷酸铁锂前驱体进行煅烧。通过精确控制回转窑的温度、转速和物料停留时间等参数,使磷酸铁锂前驱体在窑内充分反应,生成高质量的磷酸铁锂材料。该企业通过优化回转窑的工艺参数,使磷酸铁锂材料的比容量达到160mAh/g以上,循环寿命达到2000次以上,产品性能达到了行业水平。此外,该回转窑还配备了余热回收系统,将煅烧过程中产生的余热用于预热进料和干燥物料,降低了生产过程中的能源消耗,提高了生产效率。常州中温回转窑生产厂家
文章来源地址: http://jxjxysb.mjgsb.chanpin818.com/zzjrclsbfg/gongyeluyu/deta_27536587.html
免责声明: 本页面所展现的信息及其他相关推荐信息,均来源于其对应的用户,本网对此不承担任何保证责任。如涉及作品内容、 版权和其他问题,请及时与本网联系,我们将核实后进行删除,本网站对此声明具有最终解释权。